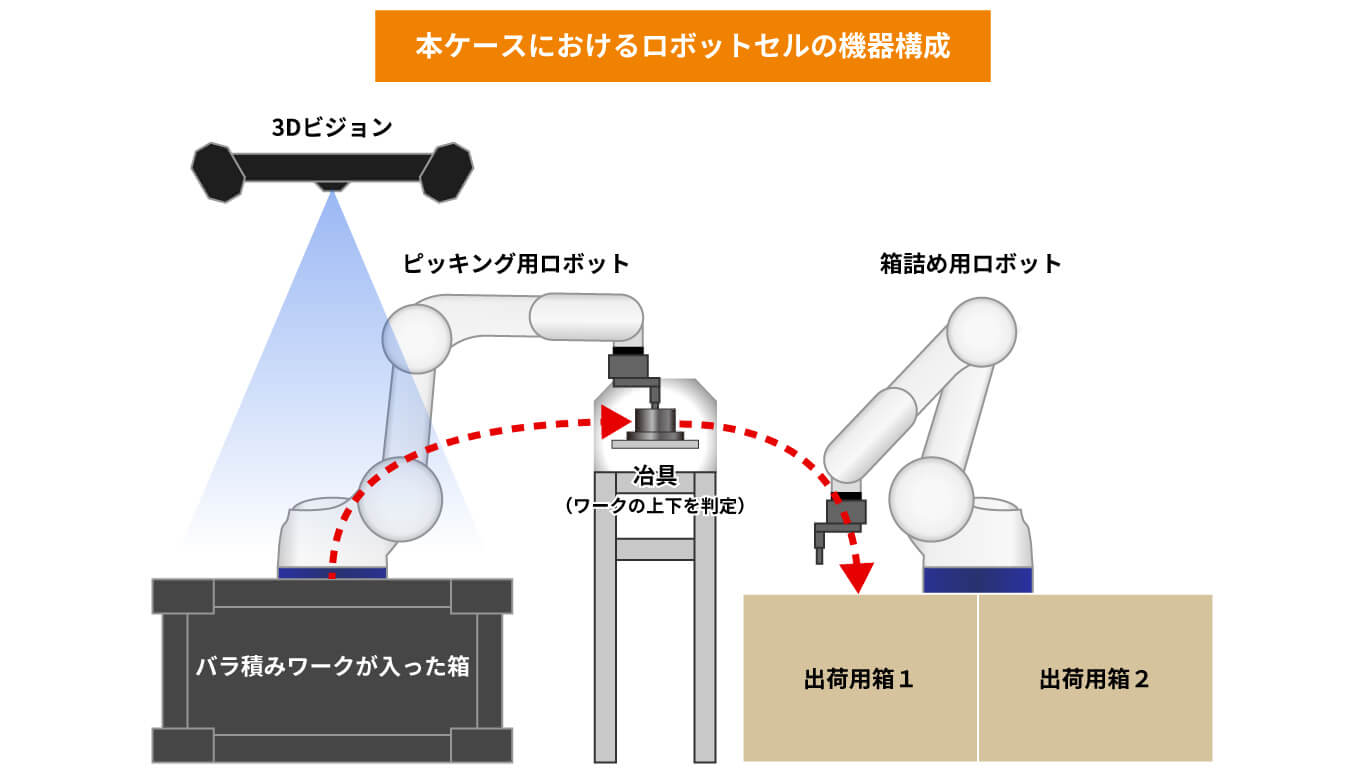
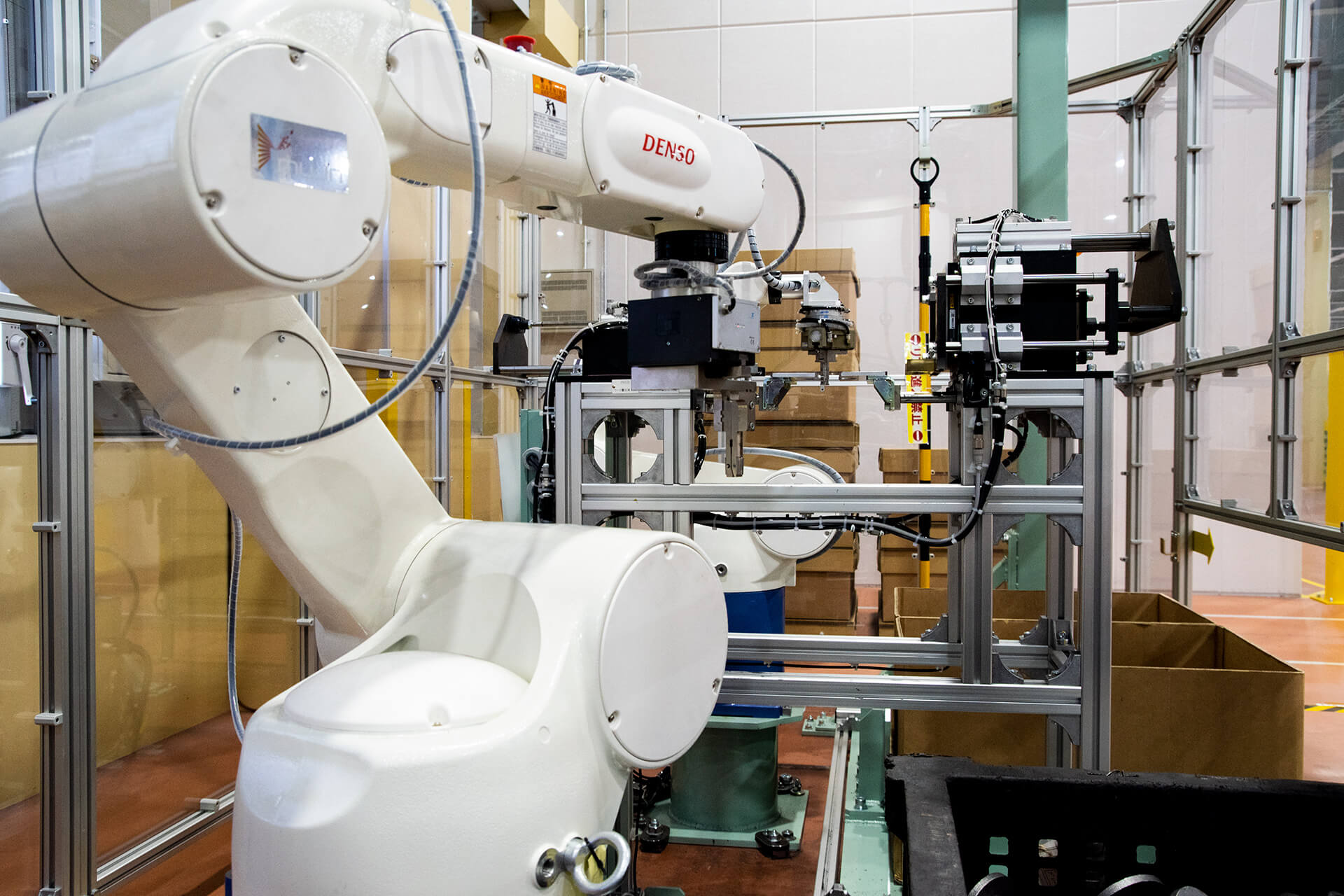
ロボット導入の概要
本ページは、株式会社アイシン様へ統合される以前の2018年に、アイシン・エィ・ダブリュ株式会社様への取材をもとに作成されました。企業名のみ変更しており、掲載内容は2018年当時のものとなります。
オートマチックトランスミッション事業でシェア世界1位を誇る株式会社アイシン様。同社の物流センターでは、作業者の身体に負担の大きい作業を、ロボットに代替させることを目的として、Mujinコントローラにて制御されたロボットが、複数種類の形状が異なる部品をピッキングするシステムを導入しています。その導入の背景には、限られた工程をロボットに担わせるだけではなく、最先端技術を積極的に採用し、社会に影響を与える新技術の開発を推し進めていく、ものづくりのリーディングカンパニーとしての矜持がありました。
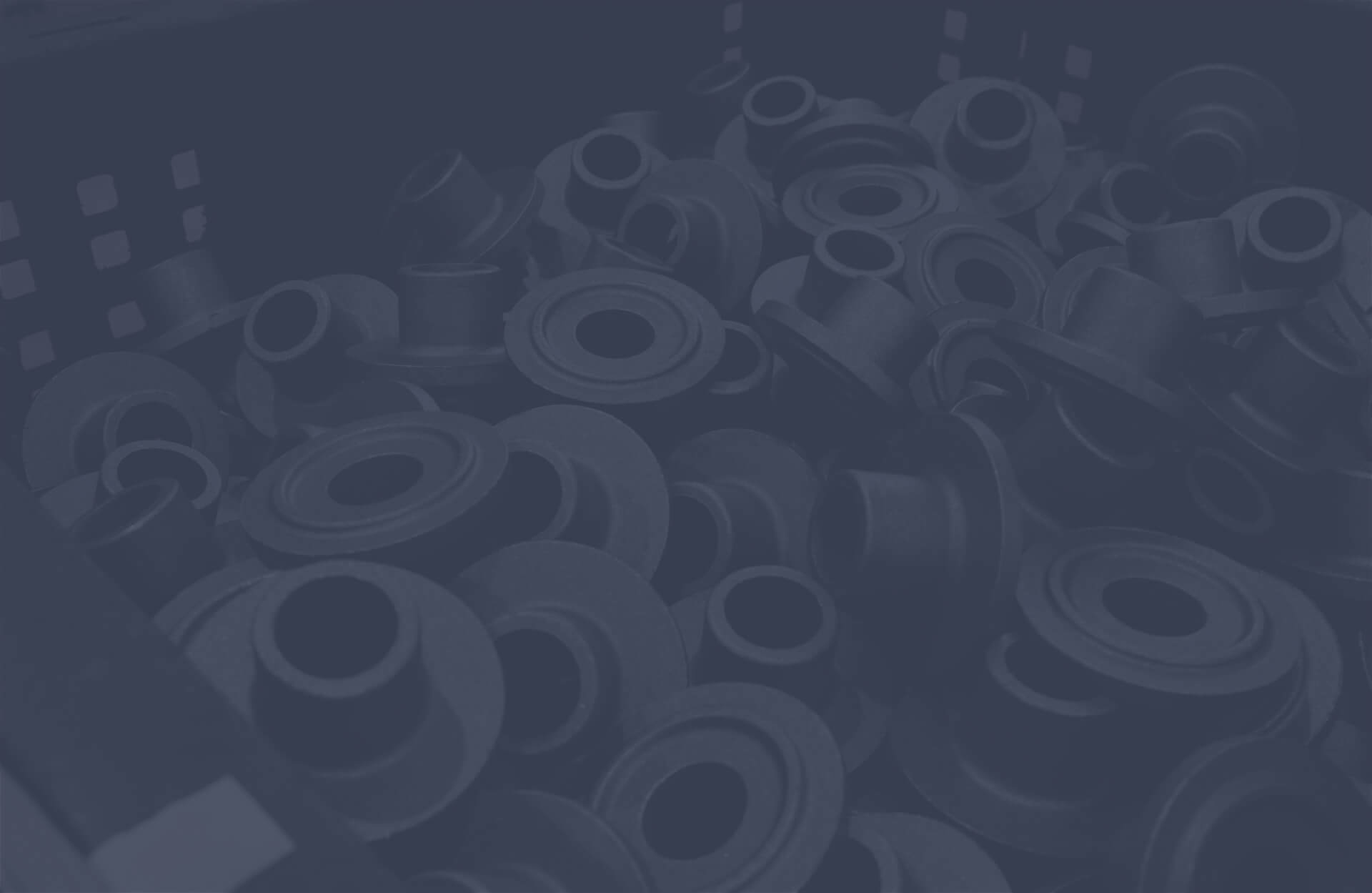
01. 課題
バラ積み状態・形状が違う複数のワーク
設備の最小化・既存設備の利用
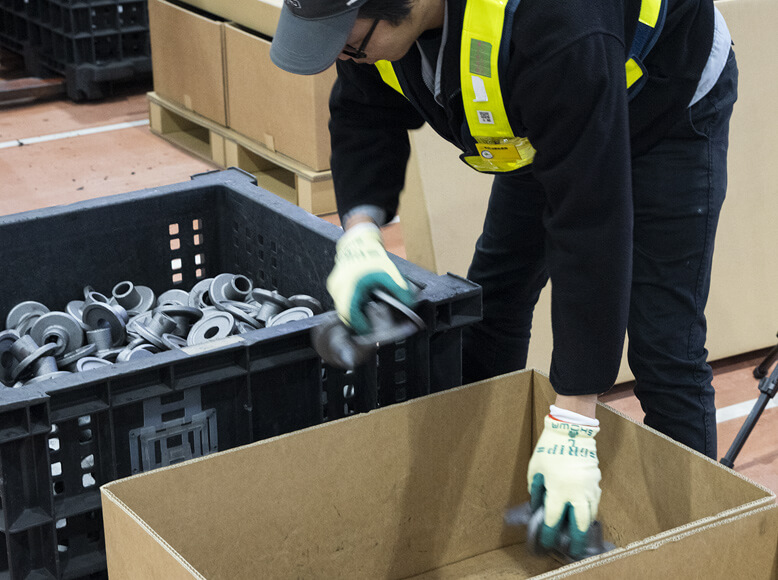
“様々な条件を考慮していく中で、唯一残された手段はMujinコントローラ”
最先端技術を積極的に採用し、新技術の開発を進めてきた同社が、なぜ物流センターにおいてMujinコントローラを採用するに至ったのでしょうか。自働化技術グループ 松山様に経緯を聞きました。
松山様:
ロボットにより代替することになった工程は、納入された金属部品を海外出荷用の箱に移すという単純作業です。それぞれの部品は形状が異なり、また重いものでは4キログラム以上あります。元々はこの工程を人手によって担っていたのですが、作業時間・合計取り扱い重量などの規定に則り作業を行ったとしても作業者の身体への負荷が大きく、離職率が高い状況が常態化していました。
もちろん様々な代替手段は検討してきており、候補には反転機やその他のロボットもありました。反転機をテストした結果は、部品の傷・打痕がひどく、製品の品質基準を満たすことができませんでした。また、規定を超える騒音の問題もあり、作業者の耳への負荷も考慮し採用できませんでした。
その他のロボットも評価しましたが、本ケースのように重い金属部品を扱おうとすると、通常のバラ積みピッキングで使っている長い爪のハンドは把持力不足になってしまう上に、遠心力に耐えるためには大きなロボットが必要になってしまいます。
そのため、いかに「小さいロボット」に「小さいハンド」で対応させるかがポイントになるわけですが、その場合はロボットが製品の詰まった深い箱に潜り込んでいくという動作が必要になります。その時にはロボットが箱内部で干渉回避ができることが必須となり、唯一残された選択肢としてMujinが浮上する結果になりました。
また容器などの設備は既存のものをそのまま使用できるというのも重要な条件です。ロボット導入のために関連する設備を変更することは、製品の価格にも影響してしまうので考えづらいことです。新規の製品であればまだ調整の余地はありますが、既存の部品のために見直すことはありえません。
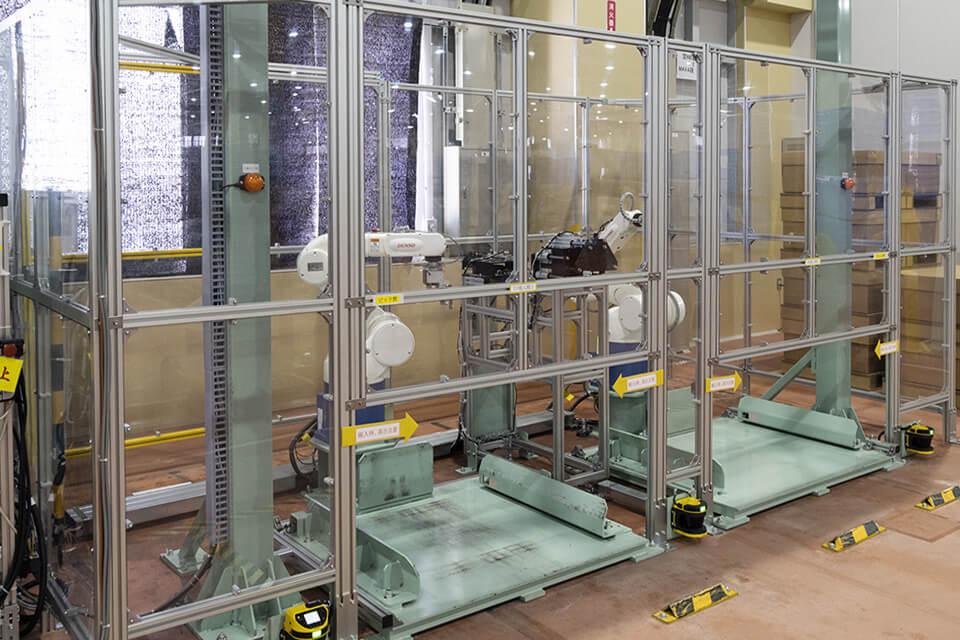
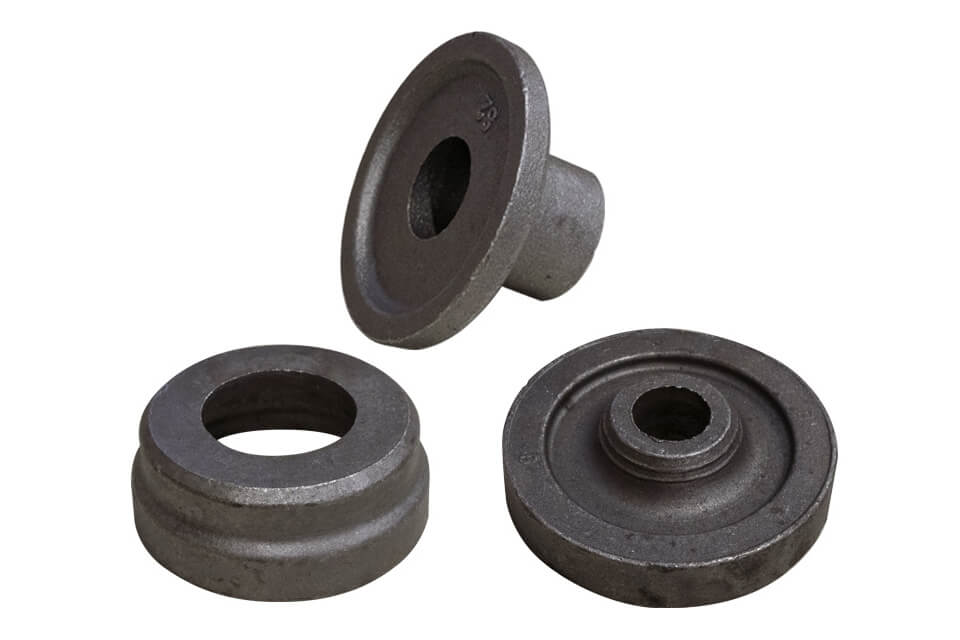
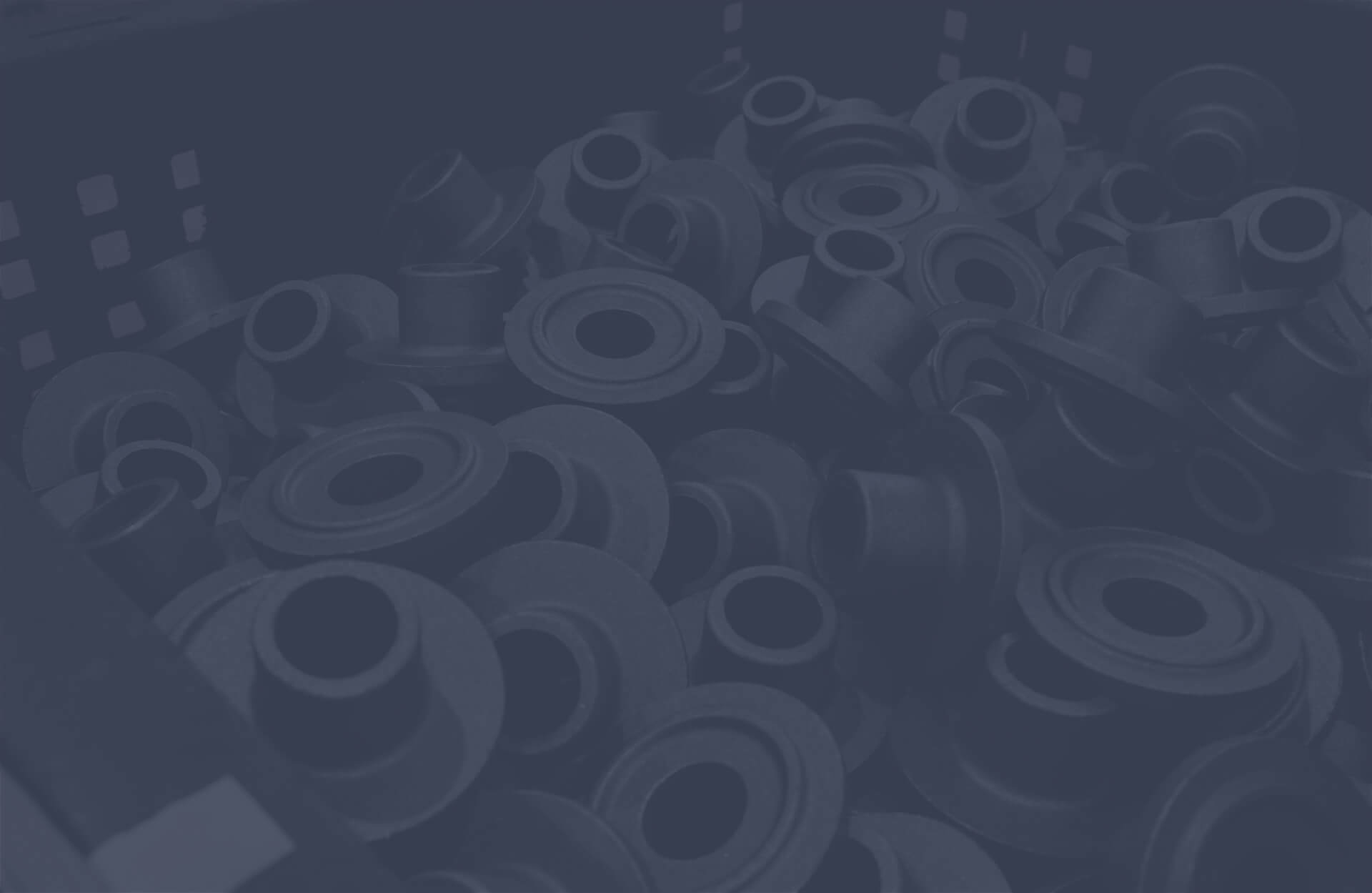
02. 解決
Mujinコントローラで工程目標のタクトタイムを達成
最小限しか人が関わらない運用体制を実現

“バラ積みピッキングは難易度が高いと言えど、失敗しても如何に止まらず作業を続けるかが肝要”
松山様:
Mujinと緊密に開発を進めた結果、工程設計の目標値となるタクトタイムをクリアしながら、深い箱の隅に残された製品までロボットでピッキングできています。どうしても物理的に取れない状況もあるので、そのような場合は作業者が対応しています。実際にはロボットに荷崩しをさせて、ピッキングし直すという機能もMUJINに組み込んでもらってはいますが、それを行ってしまうとタクトタイムが間に合わなくなってしまうので、製品の残り個数が少ない時は、実施しない設定にしています。箱が満杯の状況、製品が少なくなった状況で一回一回のタクトタイムは違う結果となりますが、トータルすると狙い通りの数字が出ています。
一箱を移し替えるのに1時間半くらいのサイクルになりますが、何より重要となるのは、その1時間半の間に一切人が関わらないということです。そのためロボットが、如何に止まらず、失敗しても作業を続けるかが肝要で、1時間半、2時間など決まったサイクルで動き続ける必要があります。改善を継続した結果、理想に近い形に近づいています。
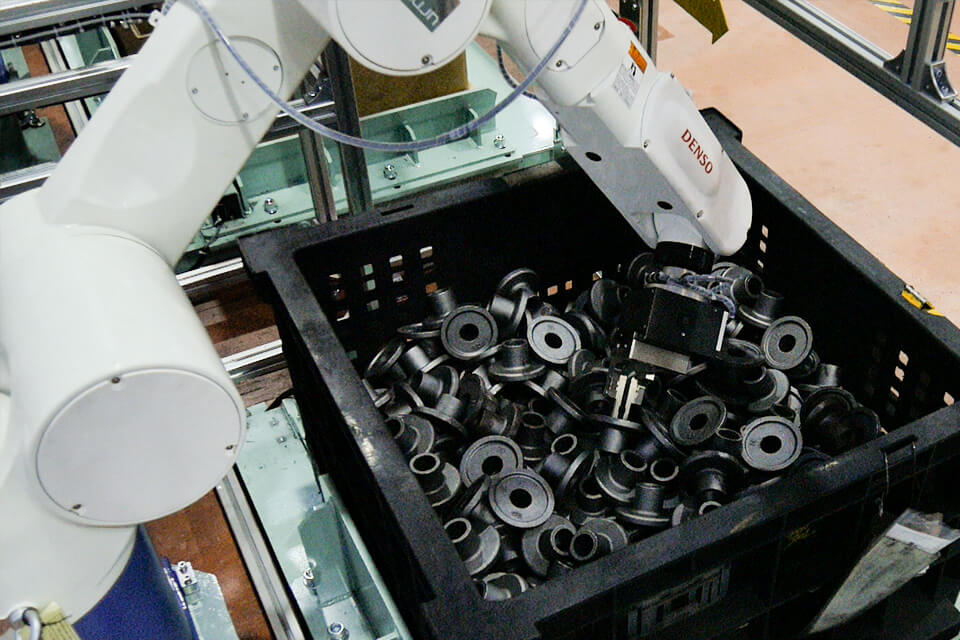
ワークがバラ積みされた深い箱からも正確に把持
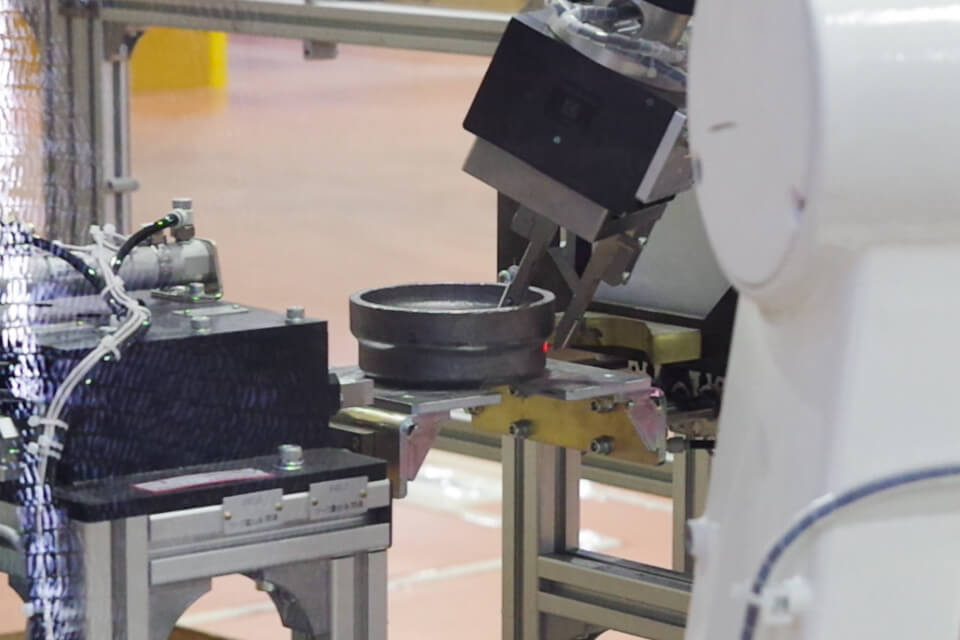
冶具を中継し、もう一台のロボットが箱詰め
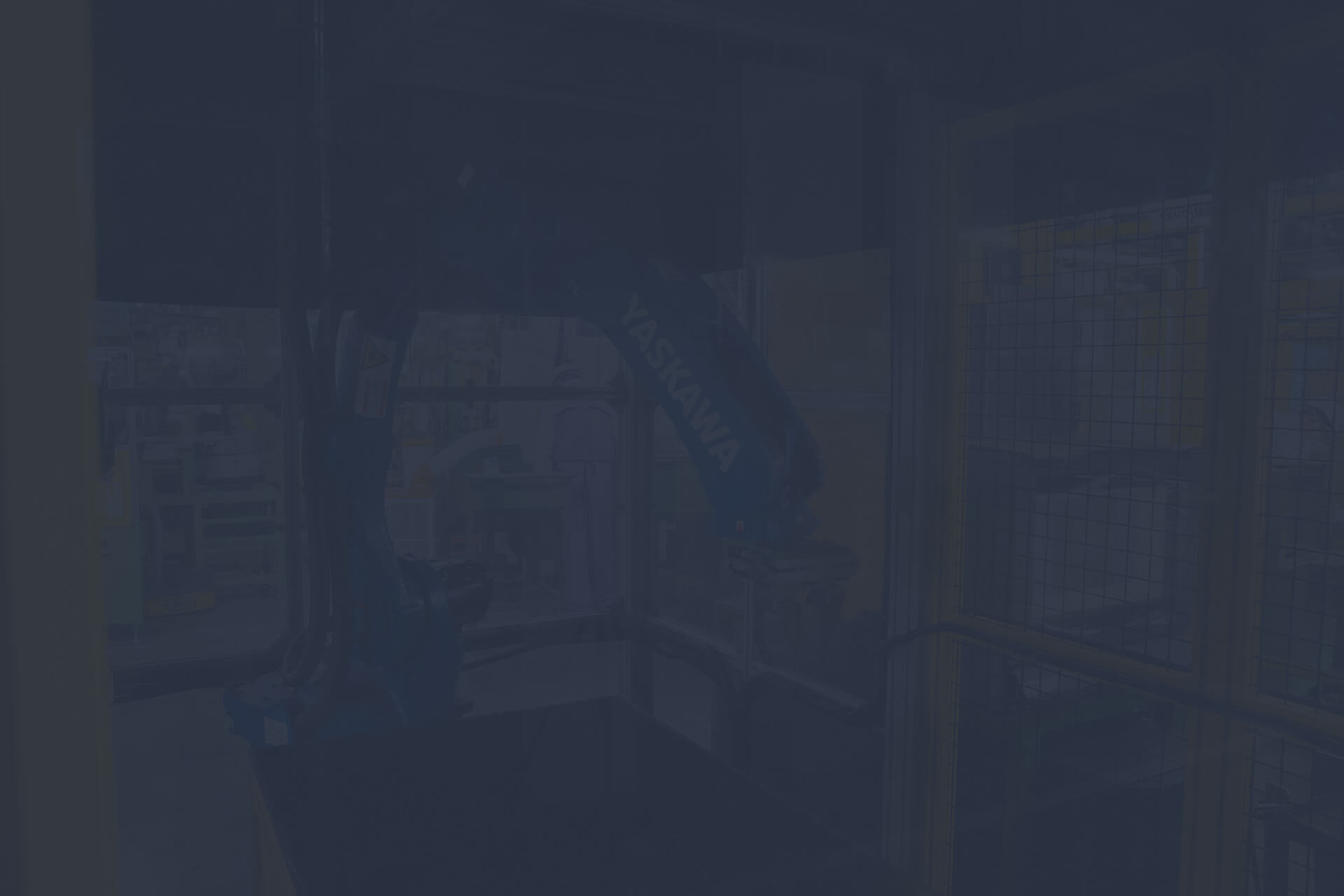
03. 運用
簡単な操作のみで形状・重量の違う4品種のワークを運用
より機能を拡充した後継機の開発も進行中
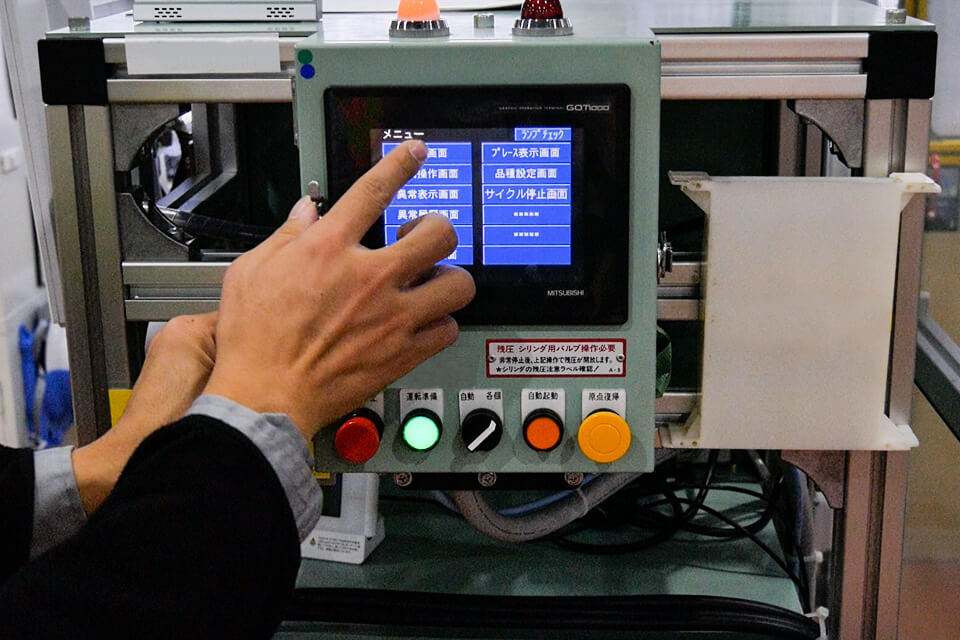
“物流センターの稼働状況に柔軟に適応する、後継機の開発にも目処が立ちました”
松山様:
現在5~6人の作業者が設備の運用、管理をしています。基本的には制御盤の操作となりますが、異常があった際には、ジョグ運転でロボットを逃がして、ワンタッチで原点復帰させるなど、運用上必要な操作は全員がマスターしてます。
現在運用しているロボットは、技術開発のベースとなった1号機という位置づけになります。発展型の2号機の開発も進んでいて、より幅の広い荷姿、重さに対応する技術的な目処がたったところです。1号機では4種のワークを扱っていますが、2号機では新たに5種のワークを扱う予定です。さらに2号機では、1号機で取り扱っている4種のワークも取り込めるように検討を進めています。部品の発注が散発的になったとしても、数多くの品種を1台のロボットで扱うことができれば、発注のバラつきを吸収できるようになります。ハンドチェンジだったり環境の切り替えなどの機能を付与して、出荷荷姿に合わせて段ボールに中敷きを敷くといった、組み立てのような作業までMujinの技術を活用して順次担わせていきたいですね。
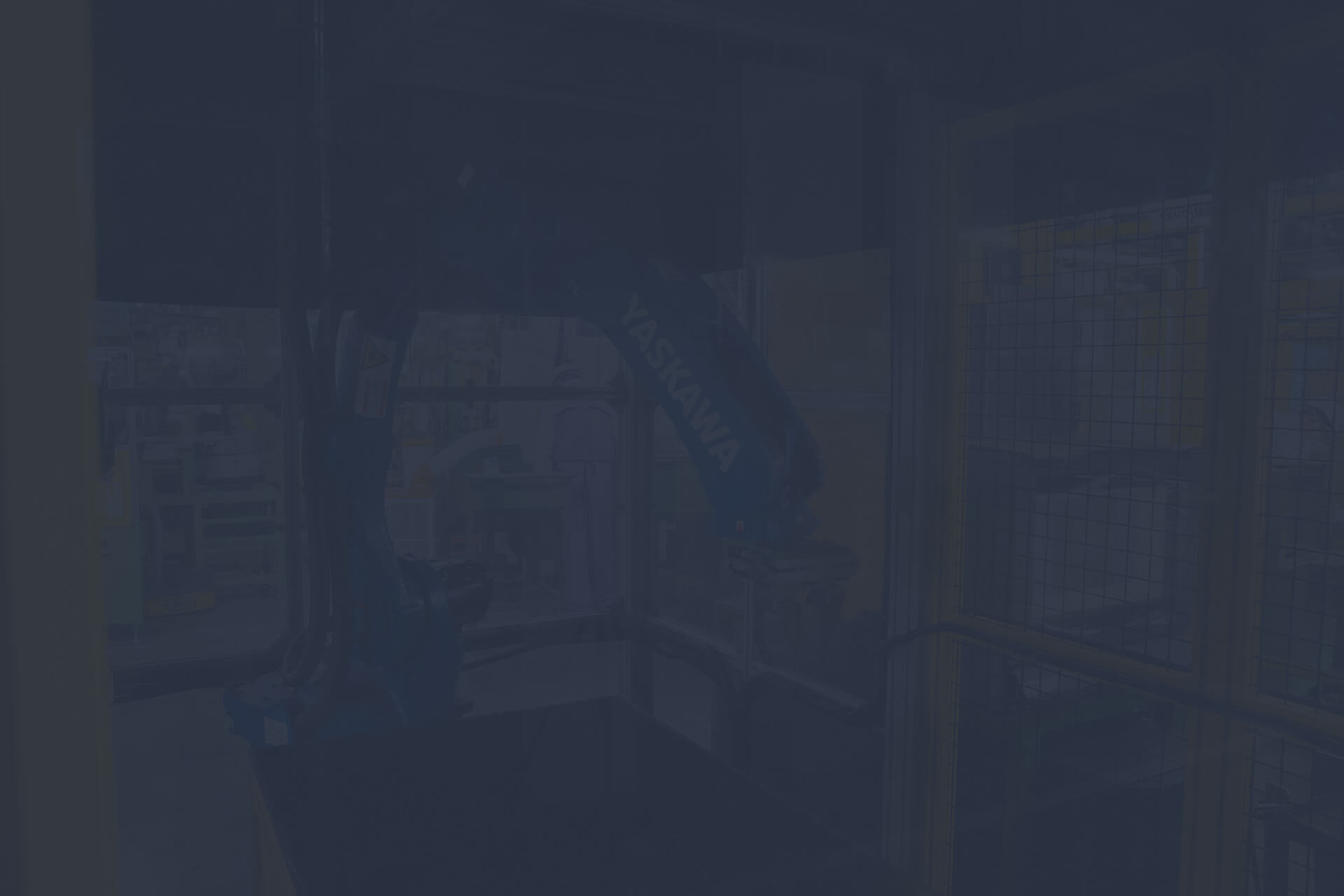
04. Mujinとの共同開発について
さらなる機能向上のために緊密かつ迅速な開発体制を継続
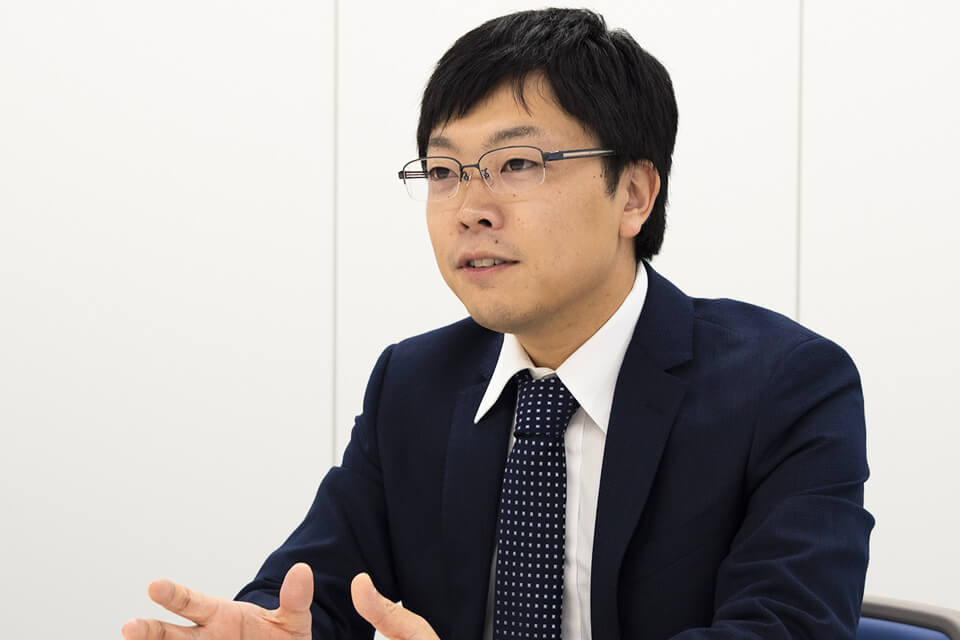
“我々が新技術開発を提案し、Mujinが実装するという体制を継続していきたい”
Mujinとの開発においては、自分たち自身でMujinコントローラを使いこなし、技術を知ることからスタートしました。ロボットに対する知識がなければ、当然プロジェクトを自分たちで主導することができないし、知ることが導入までの最短の道のりと考えた結果でした。技術的な対話ができるという信頼関係が第一です。すべてお任せして解決策を持ってきていただくという手法が一般的かもしれませんが、そのような手法ですと開発もなかなか前進しないし、スピードも上がらないと考えています。
共同開発に際しては、ただ一口にロボットを扱うといっても、3DビジョンやPLCなど周辺機器との連携が必須で、多くのFA的な知識も必要な上、3D CADも扱うということもあり、これらに習熟していない担当者がいきなり対応できるものではなかったという印象を持っています。高い品質保証が必要な号口生産において運用していくにあたってはかなりの知識が必要だと感じています。
開発を進める中で印象に残ったこととして、既存の機能だと解決が難しいという状況があった際に、1~2日後に改善策を提案してくれたことがありました。さらに言えば、課題解決を考慮した上で、より汎用性の高い技術を提案いただいたという結果になり、Mujinの技術的な実現力、エンジニアのパワーを感じました。こういった新機能の開発というのは、通常数カ月から半年、場合によっては1年以上かかることもありますし、「次のアップデートまで待ってください」と言われるケースもあります。必要な知識の膨大さ、技術の難しさは感じていましたが、これだけ短期間でアップデートしてくれるというのは、これから共同開発をしようという状況では心強かったですね。
結果として現在の開発体制には満足しています。今後も新機能を我々が提案して、Mujinが実装するという形で協業していきたいと考えています。前述の通り我々の問題を解決しつつ、より汎用的なものへアップデートしていくという流れができているので、今後も密に連携しながら進めていきたいですね。ただ現状でも工程設計の目標値はクリアしているものの、Mujinのポテンシャルを考えると、実際稼動しているロボットのタクトタイム、失敗率、リトライの回数はまだ改善する余地があると思います。より早く、より正確に、より失敗なく動作できるよう、我々の知見やノウハウも加味して新技術開発の提案をし、それに対してMujinに新機能を実装していただき、より良いものをつくりあげていきたいですね。
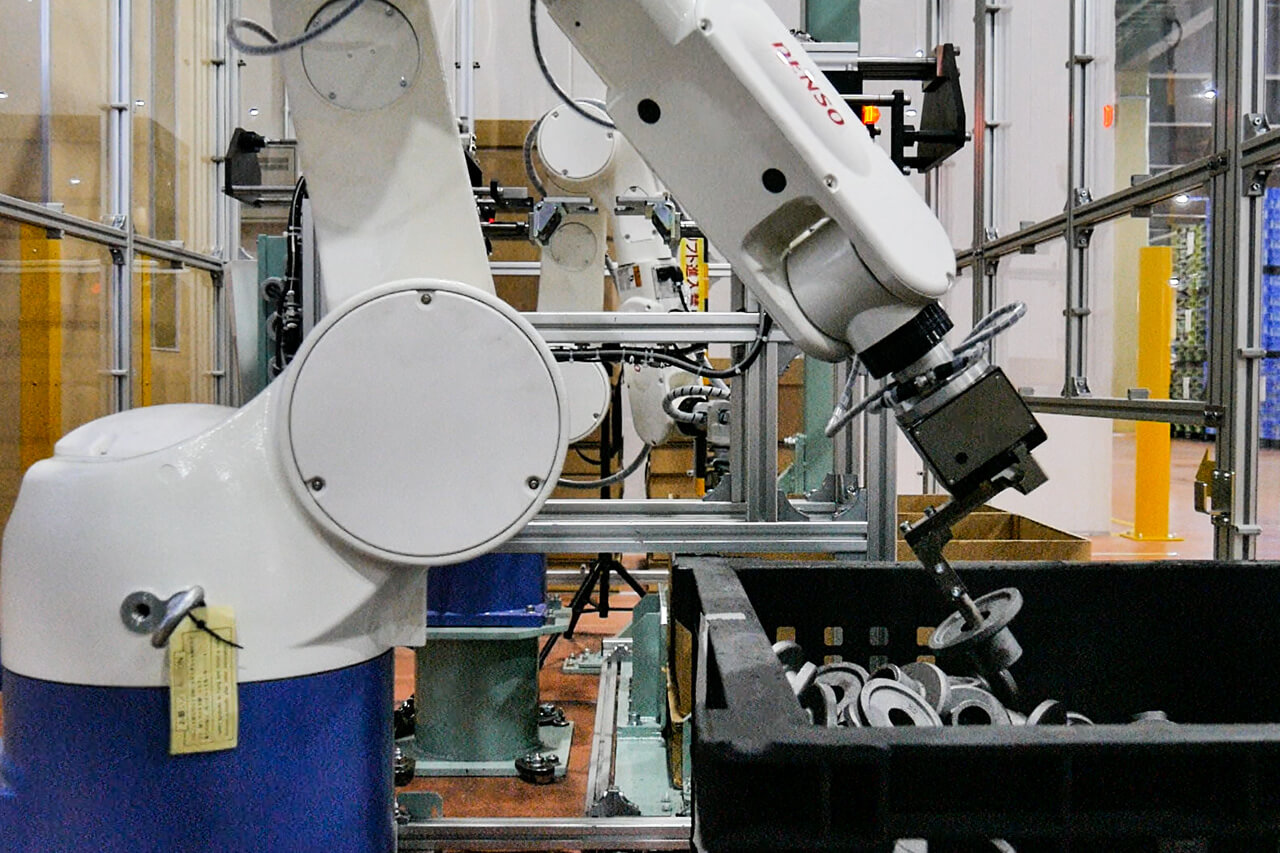
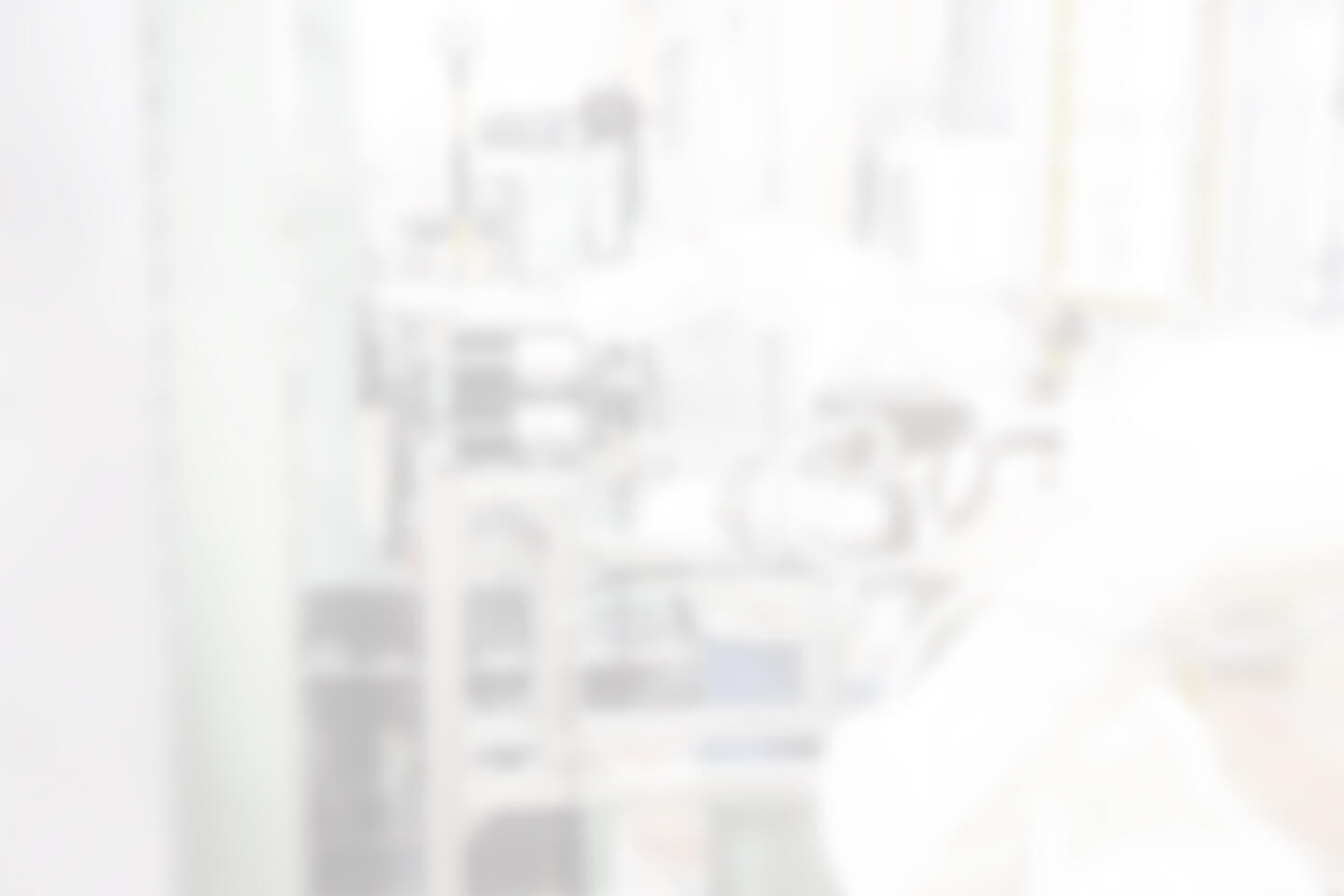
リーディングカンパニーとしての提言
株式会社アイシン
松山 孟司 様
我々とMujinのようにオープンに開発を進める手法が、
ものづくり全体としてのレベルアップへ繋がる
現状はひとつのアプリケーションとしてバラ積みピッキングを使用していますが、Mujinの技術を活用して、より多くの要素をティーチレスで実現することが、ものづくり業界に身を置くものとして、重要になってくると感じています。今後は多品種少量生産が主になってくると思うので、多品種に対応しようとなると、品種ごとにティーチングするということが非常に困難という側面もあります。
ティーチングマンにはその人なりのプログラムの方法があり平準化が難しいですし、一朝一夕に習得できるものではありません。これから自動化が一気に進んでくる状況になると思うので、その中でティーチングマンに頼らざるを得ない状況が続くと自動化が追い付かない可能性があります。そのため、ティーチレスで簡単にロボットを立ち上げられるというのが重要で、その中でより安く高品質なソリューションが求められると考えています。
労働人口が毎日2000人程度減っていると言われている現状において、いかに自動化を進めていくのかという中で、ティーチレスで動作するロボットの担う役割はますます重要なものになります。
開発においては、各社がブラックボックスで情報を閉じてしまうと、ものづくり全体としてはレベルアップが難しいと感じています。情報が閉鎖的な環境では現状に満足してしまったり、他社からの情報も入りづらくなってしまいます。我々とMujinのようにオープンに開発を進める手法が重要です。現在は自社に向けての開発が中心ですが、業界全体を考慮した新機能・新技術を開発していかないと、先々で行き詰る懸念があります。気づいた時には海外から新しい技術が入ってきたり、外資系の企業に全部さらわれてしまう恐れもあるでしょう。
Mujinのバラ積みピッキングというソリューションは、業界を超えていく技術です。例えば、食品、産品、電子、電機。他業種とでもグループを形成して技術を共有していく必要があります。技術開発が進んでいる大手企業が、ものづくりのリーディングカンパニーとして、何かを成し遂げることができるといいですね。それはトヨタグループなのかアイシングループなのか、愛知県など自治体単位、はたまた日本のものづくり全体なのか、業界や地域を越えて協力していかないと成立しないものです。
労働人口も減少して、人が集まらないという問題が現在以上に表面化する時代が来るでしょう。開発という観点からは、30年後の未来に責任をもって現状を判断する必要があります。そうしないと将来表面化してくる問題を問題とすら認識できません。もちろん製品を作る以上、コストを下げなければという側面はつきまといますが、現状において効果が小さいからと言って開発を進めないのではなく、将来を見越して必要な投資は積極的にしていくべきです。
人がもっと効率的に、人ならではの仕事を担うところがあると思うので、難易度が高いとしても人手で担う必要がない工程から徐々に自動化していく必要があるのではないでしょうか。業界を主導する立場としてまずは我々がやってみる。そしてうまくいけば世の中に広く展開していくことが重要だと思います。そこをブラックボックスにしてしまうと、我々が良くても全体として経済は悪くなってしまうでしょう。オープンイノベーションで全体的な底上げができなければ長期にわたって競争力を維持できません。